Personal Protective Equipment at Work: Health & Safety Guide
What is Personal Protective Equipment?
Personal protective equipment is any equipment or clothing used or worn to protect a worker against health and safety risks. Hazards include physical, environmental, chemical, and bio-hazard risks.
What Does PPE Protect You From?
PPE can protect the lungs, eyes, head, feet, skin, or body – depending on what you wear. It protects you from work-related dangers, including:
- Contaminated air.
- Skin infections.
- Cuts and punctures.
- Impacts.
- Chemical burns.
- Electric shocks.
- Extreme temperatures.
- Projectiles that could harm eyes.
- Entanglement in machinery.
Where occupational hazards like these exist, the employer must carry out a risk assessment and determine how to reduce or eliminate risks. They will first try means such as control measures and safe working systems to eliminate or reduce the risk.
However, if these do not reduce the risk sufficiently, personal protective equipment will be issued as a last resort to protect workers from dangerous work activities. In some situations it will always be necessary to wear PPE, e.g. hard hats and hi-visibility clothing on construction sites.
Who Is Responsible for PPE?
Employers should provide suitable PPE for work. Employees do not have to pay for necessary PPE – employers must cover the cost. They must also train employees in how to use it. Equipment should be readily available or there should be clear instructions on where to find PPE.
Employees must maintain their PPE and report faults to their supervisor or manager immediately. Even a small crack or tear can be enough to compromise safety.
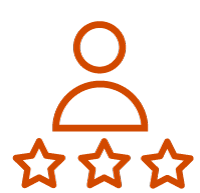
Need a Course?
Our PPE Training is designed to familiarise employers, senior staff, and employees with all the fundamental aspects of PPE that is used in work environments. With this knowledge, learners will be fully prepared to select and use PPE properly so health and safety is upheld at work.
PPE Selection
Employers should choose PPE with careful consideration.
- Pick PPE that is appropriate for the specific hazard(s) to which users are exposed. For example, if an employee works in wet conditions, safety boots must be waterproof.
- If multiple items of PPE are needed, make sure they are compatible. For example, if workers need hard hats and need noise reduction equipment you need to make sure they can be used together.
- Make sure the PPE is suitable for its user. PPE must fit workers correctly, so be sure to choose suitably-sized high visibility jackets for smaller and bigger individuals.
There will be various other factors worth considering – depending on the workplace, of course. If in doubt, the employer should ask the supplier for advice on the different types of PPE available.
Maintaining PPE
Damaged PPE is ineffective, and it can place workers in great danger. Therefore, it is essential to maintain.
What to consider when maintaining PPE:
- Store equipment in a dry, clean cupboard or storage box/case.
- Keep equipment clean and in good repair.
- Pay attention to the manufacturer’s recommended maintenance schedule.
- Pay attention to the recommended replacement periods and shelf lives.
Most importantly, users should check their PPE every time they are about to put it on and when they put it away. They should report any obvious faults immediately and remove the faulty PPE from access.
Further Resources:
- PPE Quiz
- RIDDOR: How to Report an Accident at Work
- Hard Hat Colour Codes in Construction: What Do They Mean?
- PPE in Construction: Safety Guidance and Checklist
- PPE Training